Thomas Frid, Engineer
Thomas Frid at Vallviks Bruk, is both an Automation Engineer and an Instrument Designer. He and the department work in many strategic projects that contribute to the modernization of the facility, with greater reliability and safety.
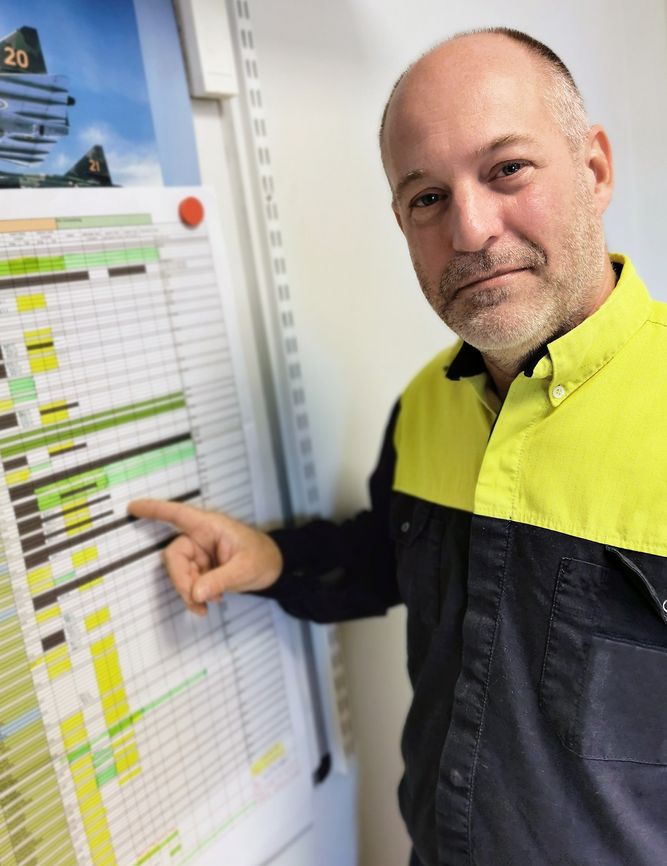
"If you make an analogy with the human body, you could say that the electrical department is the muscles, systems are the brain and instruments are the factory’s nervous system. Simply put, information flow." So says Thomas Frid, an engineer in the Automation Department.
Who works at Instruments?
“There are six of us in the Automation department at Vallvik Mill, with Tord Andersson as Manager. The department includes Systems engineers, Planners and Electrical and Instrument designers. As well as Electricians and ‘Instrument makers’.”
What does Instruments do?
“Sometimes the instruments that we read and regulate are inside the process itself and sometimes outside. It’s all about temperature, flow, pressure, and level. The signals that we process go to the control systems where the system engineers take over. They call up the information on screens at the operator stations.”
In what form do you work?
“We work on a number of strategic projects, which are assigned to us and are usually finalised during the year’s turnarounds. Once we have the process solutions ready in the design phase, we select and procure control and regulating equipment in liaison with purchasing. Assembly, cabling, piping, etc. is done exclusively by external contractors in the projects. We’re also responsible for managing the instrumentation contractor in any projects.
"In the final phase of the projects and at the start-up of the factory, it’s necessary to check that everything works as intended and therefore we do a considerable number of final checks to help us verify this."
"This year, I’ve had one project of my own and 6-7 projects where I acted as sub-project manager. Normally, a project belongs to a specific factory department, but some projects span several departments in the mill.”
Can you describe your role as an automation engineer?
“I do some proactive work on what equipment we need for research and development and what research and development we need to carry out. The role involves keeping up with modern technology and advancing positions on the instrument side. It’s to my advantage that I have a large network of similar services in other mills after my years as a instrument fitter always on the road. There are opportunities to share tips and experiences.”
Can you describe your dual role as an Instrument Designer?
“I’m responsible for keeping the documentation/drawings etc. for instruments up to date in paper form and in IFS. As there are continual changes to equipment in the factory, there’s a need to update specifications and circuit diagrams in CAD, update spare parts in the warehouse and in IFS if new equipment is purchased.
Tell us about your background?
“I was born and raised in Söderhamn and studied Automation at high school. I’ve been working with instruments since my military service - as an Instrument Installer and Contractor for the paper, energy and pharmaceutical industries, for example. I was already here in Vallvik in 1989 when I worked for Siemens, when virtually the entire factory was rebuilt and the departments’ control rooms were centralised into an operations centre.
"For the next seven years before I started here in 2015, I was a supervisor at Instrumentmontage Jansson Olsson AB in Bergvik and stationed at BillerudKorsnäs in Gävle."
"So I started as an instrument designer, and now I’m employed as an automation engineer. A new instrument designer position was never created, so those tasks fall to me as well."
Has your role changed in the years you’ve been here at Vallvik Mill?
“We’ve moved forward in many ways, such as in terms of modernisation and increased reliability of the plant. We’ve also gradually revamped the factory to ensure safer research and development where there were previously risks in the work steps.
“I’ve also been lucky to come here at a time when a lot has been invested in the factory, partly to meet the more stringent environmental requirements of the future.”
What’s the most fun part of your job?
“Having the opportunity to influence and contribute with my knowledge and the positive vibes about the possible factory development in the future."
"I think we’re a good team here at Automation, and Tord is a great manager.
He keeps the group together and makes sure we’re all pulling in the same direction.
We’re good at giving each other feedback.”